FDA Enforcement of Dietary Supplement cGMPs
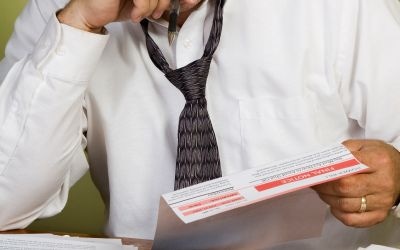
While FDA's release of the Draft Guidance on New Dietary Ingredient (NDI) Notifications in July 2011 created a lot of discussion in the dietary supplement industry during the last seven months, compliance with the dietary supplement cGMPs (current good manufacturing practices) has generated its own fair share of attention from industry. Published as a Final Rule in 2007 (21 CFR Part 111), compliance with cGMPs for dietary supplements became mandatory for all companies in June 2010. With the increase in FDA inspections as a result of the Food Safety Modernization Act (FSMA) and the intent of FDA to ensure compliance with the cGMPs, dietary supplement companies must familiarize themselves with the cGMPs and implement all of the provisions or risk escalating regulatory action from FDA.
Inspections
Promoting compliance with the cGMPs was clearly at the top of the FDAs enforcement agenda in 2011 and will continue to be a priority in 2012. A review of the warning letters issued in just the final quarter of 2011 reveals FDAs focus on the industrys compliance with cGMPs. Of the 165 posted warning letters dated between Oct. 1, 2011, and Dec. 31, 2011, almost half of those letters, 79 in total, were issued for alleged violations of cGMPs, with 44 issued to food companies, 18 to medical device companies, 12 to dietary supplement companies and five to pharmaceutical companies.
All of those letters were issued subsequent to inspections conducted by FDA in which numerous alleged violations of the cGMPs were observed by FDA investigators. Alleged violations are identified as observations in an FDA Form 483, which is issued at the conclusion of an inspection. The FDA Form 483 does not constitute the final agency determination; instead, the FDA Form 483 is considered along with a written report from the investigators, other information gathered on-site and any responses provided by the company. One point made clear in the warning letters issued to dietary supplement companies: it is in a companys best interest to provide a comprehensive response that details how the company is going to address and correct the deficiencies noted in the 483 report. While a company is under no obligation to provide a response, FDA encourages companies to do so. In each of the warning letters issued to companies for cGMP violations, FDA identified inadequate responses and the failure to provide supporting documentation from companies as, at least partly, the reason for the subsequent issuance of warning letters. An appropriate response to the FDA Form 483 that sufficiently details a companys corrective actions could make the difference between the matter being handled relatively quietly or the issuance of a warning letter that is posted for everyone to read.
Warning Letters for cGMP Violations
While its easy to state that a company can ensure compliance by following each and every regulation set forth in Part 111 of 21 CFR, the practicality of compliance is often more difficult. It can be instructive to see which issues other companies have experienced in trying to comply with the cGMPs. Following are some of the more frequent sections of the cGMPs and the corresponding violations cited in the warning letters to dietary supplement companies in the last part of 2011.
Specifications
One of the oft-cited violations identified by FDA in warning letters sent to dietary supplement companies is the failure to establish the specifications listed in 21 CFR 111.70. Specifically, 21 CFR 111.70 mandates specifications must be established in a number of areas, including specifications for steps in the manufacturing process, component specifications, in-process specifications, specifications for labels and packaging, and finished batch specifications.
Additionally, 21 CFR 111.75 identifies the duties companies have to ensure such specifications have been met. Among other violations, companies have been recently cited for failing to conduct appropriate tests to verify the identity of dietary ingredients and failing to establish the reliability of the suppliers Certificate of Analysis (CofA).
Master Manufacturing Records (MMRs)
Several companies were cited for failing to prepare and follow a written MMR for each unique formulation of a dietary supplement that is being manufactured, as required by 21 CFR 111.205. Additionally, 21 CFR 111.210 provides the specifics that must be included in each MMR. Several companies were cited for the failure to include information such as the identity and weight of each dietary ingredient to be declared on the Supplement Facts label, a description of packaging and a representative label, and written instructions and procedures for sampling.
Batch Production Records (BPRs)
Dietary supplement companies, pursuant to 21 CFR 111.255, must also prepare a BPR every time a batch of a dietary supplement is manufactured. Companies must provide complete information relating to the production and control of each batch manufactured; that necessary information is spelled out in Section 111.260. In a letter dated Nov. 1, 2011, one company was cited for at least nine different failures to include the information required, including the identity of equipment and processing lines used in producing the batch, the lot number assigned for each ingredient and documentation showing quality control personnel reviewed the BPR.
Additional Violations
Additional violations included the failure to identify qualified quality control (QC) personnel (21 CFR 111.12), the failure to keep records of training personnel for compliance with the cGMPs (21 CFR 111.14), the failure to keep records for calibrating and cleaning equipment and utensils (21 CFR 111.35), the failure to properly quarantine components of dietary supplements prior to using them (21 CFR 111.155), and the failure to establish and follow procedures for reviewing and investigating product complaints. In one case that can only be characterized as either a complete lack of knowledge of or an utter disregard for the cGMPs, FDA observed the principal of a company walking through the warehouse and packaging and labeling area during the FDA inspection with a dog in her arms, in clear violation of the prohibition contained in 21 CFR 111.15(d), which mandates no animals or pests are allowed in any area of the physical plant.
The above violations demonstrate the need for companies to implement compliance programs, starting with the identification of personnel who are knowledgeable and familiar with all aspects of the cGMPs. Companies must create and implement all of the components of the cGMPs and properly train employees to ensure compliance. In this manner, with inspection in the near future being a virtual certainty, companies will be adequately prepared when the FDA comes calling.
Justin J. Prochnow ( [email protected] , (303) 572-6562) is an attorney and shareholder in the Denver office of the international law firm of Greenberg Traurig LLP. His practice concentrates on legal issues affecting the food and beverage, dietary supplement and cosmetic industries.
Still Need Help with GMPs?
Find additional information about GMP compliance in the SupplySide Store, including:
An on-demand video, "The FDA Speaks on GMP Compliance"
An on-demand video, "GMP Compliance and Contract Manufacturers: The Legal View"
Visit the INSIDER Solutions Center on DSHEA to view:
A whitepaper from EAS Consulting, "Where Supplement Firms Go Wrong in cGMP Compliance"
View INSIDER's Webinars to see:
Information from FDA, the Council for Responsible Nutrition and industry consultants, "Dietary Supplement GMPs: What Can Industry Do Better?"
About the Author
You May Also Like