AstaReal American Facility Celebrates One Year
AstaReal Technologies, a subsidiary of Fuji Chemical Industries Co., celebrated its one-year anniversary on May 14, during an event that united members of the community and the company.
May 21, 2015
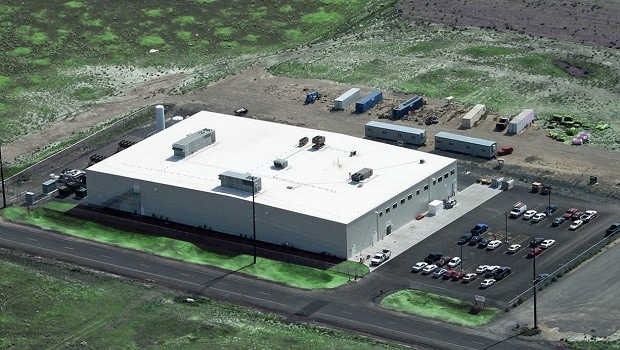
AstaReal Technologies, a subsidiary of Fuji Chemical Industries Co., celebrated its one-year anniversary on May 14, during an event that united members of the community and the company.
Construction of the astaxanthin facility, located in Moses Lake, Washington, was completed on the same day in 2014. Following the completion of the facility, 52 employees were hired from the surrounding community.
Many members of the community joined AstaReal in celebrating the facility’s successful first year; speakers at the event included Dick Deane, mayor of Moses Lake, Kyle Lynch, from the office of Senator Judy Warnick, R-Moses Lake, and Jonathon Smith, executive director of the Grant County Economic Development Council. Mitsunori Nishida, president of Fuji Chemical Industries, also spoke at the event.
Prior to the opening of the Moses Lake facility, the company was not producing enough astaxanthin to keep up with global demand, according to Charles DePrince, president of Fuji Health Science, who also spoke during the event. At that time, the company’s astaxanthin supply was coming from its original astaxanthin facility, AstaReal AB, located in Sweden. DePrince added that the Moses Lake facility will help fuel the growth of the business for the next five years. In addition, the new facility allowed for improvements in technology, and for the company to produce astaxanthin that is made in the United States.
Astaxanthin is an antioxidant-rich carotenoid that is found naturally in a variety of organisms, such as shrimp shell, crab shell and red yeast. However, as noted in INSIDER’s Buyers Guidebook, “Astaxanthin Acquisition," most commercially available astaxanthin is harvested from algae, as is the case with AstaReal astaxanthin.
Often, astaxanthin suppliers produce the initial phase of the algae in closed culture systems, and then transfer the microalgae to an open pond or bioreactor, the Buyers Guidebook noted. In the case of AstaReal, the astsxanthin is produced using a closed, isolated production system to ensure consistency and quality.
The process AstaReal uses to produce its astaxanthin is proprietary. INSIDER had the opportunity to tour AstaReal Technologies, and get an “insider’s" peek at the complex and detailed production process, which begins with the algae’s initial growth in the “culture lab"—a sterile room that’s highly restricted to prevent contamination. As the algae grows, it’s transferred to larger tanks that supply oxygen and nutrients, until it reaches the final growth stage. At this point, the algae is agitated (receives lower nutrients and higher light) to produce astaxanthin, which becomes visible via the agitated algae’s bright red color. Algae is harvested from the tank—a process that takes approximately six hours—and then is prepared for extraction.
The entire process takes approximately two to three months, according to Nicholaus Miley, culture technologist at AstaReal Technologies. He added that the Moses Lake facility harvests the astaxanthin-containing algae every day.
Interestingly, Fuji Chemical Industries is developing products for medical foods, and plans to launch a new medical foods product by the end of 2015 via its subsidiary, AstaMed, Inc., which was established in 2014.
About the Author
You May Also Like