Audits: tools to establish a robust, quality manufacturing process
Audits can be powerful tools in providing observations and feedback between a brand owner and its manufacturer, and allow for establishment of a robust quality manufacturing process.
August 17, 2018
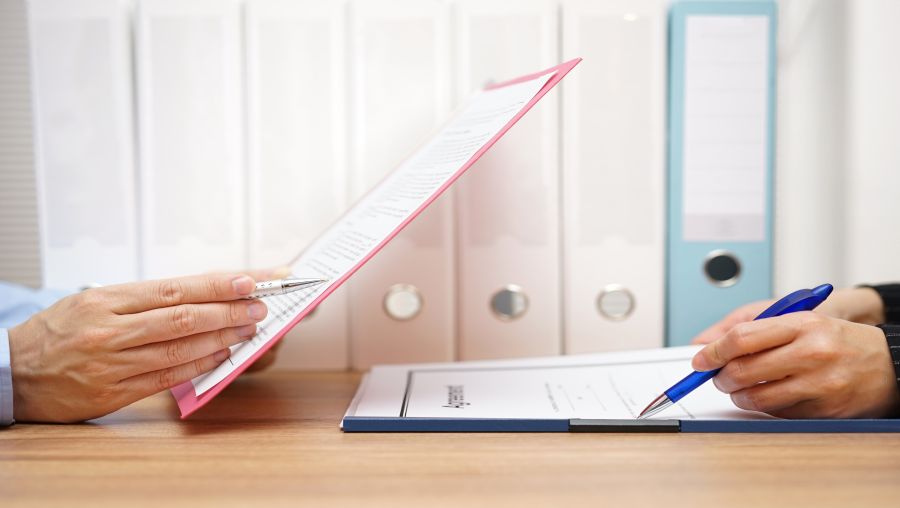
By Julie Litz
A brand has a finished good product. It has a contract manufacturer. What’s next?
Good manufacturing practices (GMPs) outline the requirements for the manufacturing of finished goods. Brand owners are charged with knowing which GMPs are relevant to a product, and then working with the contract manufacturer to draft a contract to ensure the GMP responsibilities of each company are clearly delineated. Despite using a contractor to manufacture a product, the brand owner is responsible for ensuring all contractual obligations and cGMPs that apply to the finished good are met. A contractor audit is one way of accomplishing this.
The first step of a contractor audit is to assign an auditor that is well trained in auditing based on the required specific regulations. The contract should be thoroughly reviewed, and the auditor should determine if there are any unique elements to consider when auditing the contract manufacturer. The auditor should contact the manufacturer and communicate the purpose of the audit. If available, a checklist the auditor will be using to conduct the audit should be supplied to the contractor. If the audit is unannounced, which can provide a more realistic view of the manufacturer’s day-to-day activities, the auditor should supply this information to the contractor upon arrival at the manufacturing facility.
Upon arrival to the facility, the auditor must comply with all standard operating procedures (SOPs) of the contractor while on the premises. After introductions and establishment of the framework of the audit, a comprehensive facility tour should be conducted. During this tour, the auditor should conduct a visual assessment of the relevant quality parameters. Notes of any findings should be taken during the tour and included in the final audit report.
After the tour, the auditor must conduct a thorough review of the relevant SOPs related to the manufacturing of the product. Areas and systems to be included in the document review may include:
Quality systems
Document control
Pest management
Water
Personnel hygiene
Corrective/preventive actions
Chemical handling/control
Purchasing/vendor approval
Good laboratory practices
GMPs
Food safety/HACCP
Calibration
Allergen controls
Shipping and receiving
Education and training
Traceability
Sanitation practices
Food defense
The auditor must use a formal checklist for a guide to the audit. The checklist is comprehensive and the audit may take more than one day to complete. This should be discussed with the manufacturing facility, and scheduling should allot enough time for a thorough review.
During the audit, the auditor must remember the purpose of the audit and keep in mind .she is confirming . the contract manufacturer is operating under the general premise of “Say what you do, and do what you say.” Each audit conducted is a snapshot of the manufacturing operations, and the auditor must ensure . what she is observing is reflective of the actual day-to-day operations of the plant. Questioning plant employees can be helpful in this determination.
After the audit, the auditor must write an audit report and note problems identified during the audit. These findings can be discussed in a closing meeting with all audit participants followed by submission of a written report of all audit findings to the contract manufacturer.
After receiving the audit report, the contractor will be required to respond to the findings in a timely manner. If there are any critical or major findings, the brand owner can choose to suspend the contract until the findings are resolved. All findings must be addressed by the contract manufacturer with a written plan of how they will be resolved. Representatives from the brand owner will review the written response, and if found to be acceptable, the contract will proceed. This review and response may require continual dialogue between the two companies, along with additional visits to the manufacturing facility to ensure compliance. If a satisfactory response to the audit findings cannot be established, management of both companies should get involved to resolve the differences while maintaining the terms of the contract.
After manufacturing of the product begins, audit frequency should be established. In addition to audits, the brand owner may elect to send a representative to observe the manufacturing process at the facility, which can help confirm the product is being manufactured according to the contractual obligations and the required cGMPs. This should be written into the contract and should be accepted by any reputable contract manufacturer. All appropriately updated documents associated with the audit process should be properly stored and accessible to regulatory authorities.
Contract manufacturers are essential to making finished products for many companies, and audits of the contract manufacturer can ensure quality standards are being followed. These audits can be powerful tools in providing observations and feedback between the two companies, and allow for establishment of a robust quality manufacturing process.
Julie Litz is the quality assurance/quality control director at BIO-CAT (bio-cat.com), provider of enzyme technology and custom formulations. Founded in 1988, BIO-CAT is an FSSC 22000 certified facility in Virginia featuring state-of-the-art laboratories for scientific research, product development and on-site quality testing.
You May Also Like