FDA GMP inspections: How to comply
GMP certification and compliance with FDA inspections is vitally important for our industry to demonstrate to consumers and federal regulators that our manufacturing processes are of the highest quality.
February 17, 2012
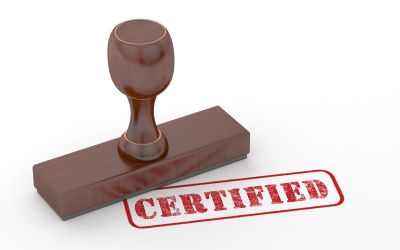
FDA has increased its regulatory activity, completing almost three times the number of GMP (good manufacturing practice) inspections during 2011 as it did in 2010. However, it's concerning that inspections have been uneven and that industry continues to struggle with compliance.
Why GMPs are important
The first GMP regulations were adopted by FDA in the 1960s. Currently, FDA has established GMP rules for drugs, medical devices, foods and dietary supplements. GMPs are generally understood to mean a system of procedures and documentation, written and/or analytical, to ensure a finished product has the identity, strength, composition and purity that it claims to possess. They define standard practices that ensure the "proactive" protection of consumers by ensuring quality is designed into a product.
GMPs establish a framework for providing a controlled manufacturing environment and documented evidence that dietary supplements are manufactured, tested, packaged, labeled, stored and distributed under conditions whereby they do not become adulterated, contaminated or misbranded. The term GMP usually includes a "c" before the abbreviation (as in cGMP) for "current" and implies they will not be static and will change as the industry evolves.
Current state of GMP inspections
FDA's dietary supplement GMPs established a phased implementation schedule that allowed companies of all sizes at least one year to come into compliance. In fiscal year 2008, FDA inspected seven companies; in fiscal year 2009, 34 companies; fiscal year 2010, 84 companies; and fiscal year 2011, 161 companies. We expect the number of companies inspected in fiscal year 2012 to increase again.
FDA stated, in fiscal year 2010, the violation rates for dietary supplement GMP inspections was nearly 25%, and it issued numerous form 483s and more than 43 warning letters, with more than 30 of those warning letters issued in fiscal year 2010. In contrast with other FDA-regulated industries, FDA would expect a failure rate of 4% to 5%, showing an obvious disconnect between FDA expectations and industry understanding. Recently, FDA took additional enforcement action with companies that are not coming into compliance, including regulatory meetings, product seizures, injunctions and even prosecution.
The quantity and the depth of the inspections has increased greatly. FDA has noted some consistent non-compliance trends emerging:
No or inadequate identity testing of dietary ingredients.
Failure to establish specifications for components, ingredients, steps and stages of manufacture and finished products.
Failure to conduct testing to ensure ingredients and products meet specifications.
Failure of adequate master manufacturing and batch production record-keeping requirements.
Failure to conduct (or inadequate) material reviews.
Lack of adequate corrective action plans.
The Natural Products Association (NPA) anticipates FDA inspections will continue to become more vigorous with a greater focus on analytical science, supplier qualification, and contaminant and adulterant issues.
Tips for compliance
Compliance is not optional and cannot be delayed; the industrys grace period" has passed. Failure to meet GMP requirements can result in products deemed to be adulterated by virtue of GMP non-compliance. The first step is to understand what GMP requirements apply to the company model; whether it involves the manufacturing, packaging, labeling, holding or distribution of dietary supplements, certain GMP provisions apply. Companies need to commit to compliance and allocate the appropriate resources to get the job done. Companies must fully understand their products, and the ingredients and processes used to make their products. Adequate and appropriate specifications for raw materials, processes and finished products are key, along with appropriate verification that specifications are met. Quality personnel are involved in some manner with all GMP-related operations; therefore, it's vital to have adequate and appropriately qualified personnel involved in quality functions.
Developing and implementing the required documentation and record-keeping is a must. Properly qualify contract facilities used for GMP-related functions to ensure they are compliant, and formalize GMP agreements so it is clear who is responsible for what. Companies should make it a priority to stay informed on quality and technical issues related to their ingredients and products, and about current FDA thinking regarding what is expected. Conduct internal audits, and use industry consultants and third-party certification programs to evaluate GMP compliance, identify gaps and institute corrective action. Remain vigilant and continually monitor GMP systems, related documentation and record-keeping to verify ongoing compliance.
Furthermore, expect to be inspected and prepare accordingly. Develop company procedures for handling regulatory inspections, have trained individuals to accompany FDA throughout the inspection process, and train all personnel on company policies related to regulatory inspections.
Jeff Wright, owner of Wrights Nutrients, a retail store in New Port Richey, FL, is president of the Natural Products Association (NPA). Wright has been active in NPA for nearly two decades, serving on the NPA-South regional board and three years on the national NPA board of directors. NPAs GMP program has certified more than 95 companies, and is based on comprehensive third-party inspections of the manufacturing facilities and GMP-related documentation to verify compliance with the requirements of NPA GMP standards. NPA also offers dietary supplement GMP education sessions
About the Author
You May Also Like