Formulation of hard-shelled capsules in supplement manufacturing
Hard-shelled capsules do not require pressing or binding, which means better absorption for high-potency ingredients. However, dietary supplement companies must carefully consider the ingredients' physical properties and flow characteristics.
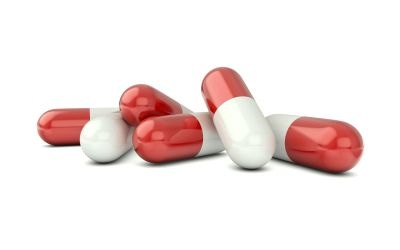
The most common form of dietary supplements is the solid dosage form. This includes tablets, capsules, and powders. Capsules are solid-dosage forms that enclose dietary supplement formulations in hard or soft shells composed of gelatin or cellulose. Manufacturers often select tablets over capsules for pricing reasons, but when all factors are considered, tablets may not always be the most economical option. Additionally, capsules offer key advantages for formulators, manufacturers and health supplement consumers. These advantages can significantly increase the likelihood of success of dietary supplements. For instance, more than 74% of consumers of herbal products prefer two-piece capsules over tablets because they are easier to swallow.
Encapsulation is an excellent choice for herbal formulas because it does not require pressing or binding. In many cases, herbal formulas contain actual plant leaves, stems or roots powder or powder extracts, which can easily be filled into capsules. In contrast, compression forces applied during tableting can contribute to decomposition or degradation of plant products. Generally, absorption is better when active ingredients are delivered in capsules. In comparison to a capsule, only 60% of a tablet is comprised of actual active ingredients. The remainder may consist of binders, lubricants and disintegrants. Tablets must first dissolve before they can be absorbed into the body. If a tablet fails to dissolve completely, this will lead to decreased absorption of the active ingredients.
Not all herbal formulas are good candidates for encapsulation. Less potent herbs that require large doses are not good choices for an encapsulated formula; these may be better taken in a powder dosage form. On the other hand, encapsulation may be the better choice for bitter tasting or mucilaginous (sticky) herbal ingredients. Encapsulated formulas may need to be taken for a long period of time or may contain herbs that should be taken in small amounts. For encapsulation, single herbs or combinations of up to three to five herbs usually work best. If there are too many herbs in a formula, the end consumer may not receive an effective dose of any ingredient. As with any delivery form, capsules have production challenges to consider. During the capsule-filling operation, heat is generated through friction. Consequently, any active ingredient with a low melting point may stick to tooling surfaces and thereby introduce potential processing and/or stability issues. Temperature and humidity control throughout the entire production may help to minimize the potency and other characteristic changes during the process. If an active ingredient is liquid at room temperature, granulation processes can be used to convert liquid or semi-liquid to granules with fillers. The liquid or semi-liquid ingredient then becomes a free-flowing powder.
Density is one of the most critical factors to consider for encapsulation. Powders with low densities may not fit into the preferred capsule size due to flocculence. Roller compaction, slugging or wet granulation can be used to increase densities of powders up to two times the original density. In some cases, thermostable ingredients may need to be heat processed in order to increase flow characteristics. Hard-shelled capsules can sustain higher temperatures which allow a wider range of ingredients and excipients to be used, including glidants and lubricants..
A glidant is a substance that improves flow characteristics of powder mixtures. Colloidal silicon dioxide, magnesium stearate and stearic acid are flow agents normally used in capsules to improve rheological properties of product powders during manufacturing. Brown and white rice flours and microcrystalline cellulose may be used as filler to deal with the tiniest of capsules. It is especially important to optimize the order in which materials are mixed together to maximize the effect of active ingredients and to ensure that the influence of lubricants is minimized.
Several excipients have limited applications, and these are specified in FDA regulations. For example, FDA regulations require that no more than 2% of a capsule-fill weight should consist of silicon dioxide. An increasing number of customers are focusing on natural or organic ingredients as opposed to synthetic ingredients. Nu-FLOW® offers producers an option to replace synthetics anti-caking agents including SiO2 with a natural or certified organic ingredient.
Hard-shelled capsules are mainly used for encapsulation and tend to feature dry or powdered ingredients. Hard gelatin capsules are made largely from gelatin, FD&C colorants, and sometimes an opacifying agent such as titanium dioxide; they also contain liquid solutions of geling agents such as gelatin and plant polysaccharides. Plant-based capsules are good for compounds that pull moisture from their environment. This helps maintain stability and extends shelf life. For example, the low water content of plant-based HPMC (hydroxypropyl methylcellulose) capsules can help prevent premature activation of a probiotics beneficial culture during storage.
Many different raw materials may be used in the dietary supplement product formulation. Gathering all required information, such as physical properties and flow characteristics, for all raw materials used in a formulation before production will help manufacturers address any foreseen problems during the production.
Jun Lin, Ph.D., is quality manager at NHK Laboratories Inc. Matthew Joseph holds a master's of pharmacy and is NHK's assistant supervisor.
About the Author
You May Also Like