Granulation: A Solution to Difficult Formulation Challenges
Adding a granulation step in the formulation process can alleviate many challenges often faced by formulators.
May 23, 2013
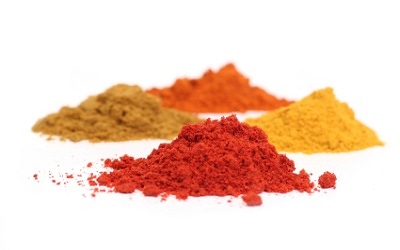
When developing a dietary supplement product, the formulator is faced with many challenges to deliver the correct quantity of each ingredient into every tablet or capsule. Non-uniform powder flow can negatively affect the distribution of active ingredients from tablet to tablet or capsule to capsule, and cause failure to meet active ingredient claims. Poor compressibility can introduce productivity problems in the tableting process. While these challenges may be faced and easily solved when formulating a simple, single-active-ingredient product, they can be much more difficult to overcome when combining multiple actives into a formula. When incorporating multiple actives into a formula, one must not only define the targeted amount of active that must be delivered in the final dosage form, but the nature and physical properties of each individual component must be evaluated, and related risks accounted for. Attention to potentially troublesome ingredient properties and inter-ingredient interactions before the formulation is created can prevent time-consuming and frustrating trial-and-error resolution of problems during finished product scale-up and commercialization.
An effective strategy for managing many of the difficult challenges is often the addition of a granulation step in the formulation. Granulation has long been known as a process where ingredients are mixed uniformly with a binder to adhere individual powder particles together and create a granulated powder that has superior physical characteristics, such as flow, to aid solid dosage uniformity. During granulation the ingredients and binder are uniformly distributed and incorporated into the granules. Because each granule consists of a blend of the individual ingredients and binder, homogeneity of active ingredients in the bulk powder, during powder flow and final dosage form can be dramatically improved. Incorporation of resinous materials in a granule can reduce or eliminate the tendency of these materials to create problems in the blending and tableting processes. Because even standard granulation techniques generally improve compressibility, the efficiency of the tableting process and often tablet hardness characteristics can be optimized.
Formulations with organically natural or naturally-derived ingredients can present a unique set of formulation challenges. The physical characteristics of these ingredients may vary due to seasonality, geography or the part of the plant from which they are derived. This variation can have a dramatic effect on the manufacturing process. The variables include, but are not limited to: density, flowability, oil concentration, particle size distribution, moisture content, and sensitivity to friction and heat. The addition of a granulation step for these products aids in the formulators ability to predict how the materials will react in the final formulation. The granulation step also allows the formulator to determine a specific set of release parameters for the granulated materials that will standardize those natural ingredient or ingredients used in the formula. This helps to minimize the inherent variations that many such naturally derived ingredients may introduce with respect to density, flow, moisture and compressibility.
Perhaps the most difficult variable for the formulator and manufacturing groups to predict and control with natural products (like certain herbs) is related to the oil and/or resin content in the material and the effect this has on blending and compression properties. Oily or resinous components can cause lumping or clumping in the blending step, requiring either a screening or milling step to overcome the issue. Milling can impact not only particle size, but density and moisture content of the blend. These properties, in turn, affect powder flow and compression. Non-uniform flow can, as stated before, create variability in the assay of the finished product. Degradation in compression properties due to milling can create issues in manufacturing with control of tablet thickness and hardness. High resin content can lead to frustration for the manufacturing group as heat generated by the tablet press causes the resin to become tacky and sticky. This can cause build up on the tablet press. Punches can break if significant build up is allowed to occur on turret, punches and dies. This creates losses in productivity as operators stop the press to clean, replace broken punches or run the press at a reduced speed in order to minimize this effect by reducing friction and the associated build up of heat.
Achieving uniformity in products that incorporate small quantities of micro-nutrients is often problematic. Formulations that require homogeneous delivery of one or more micro-nutrients in the final dosage may require the formulator to look at combining these ingredients into a larger granulated matrix. This not only ensures an even distribution within the granulated powder, but also helps minimize segregation in subsequent blending and compression stages of the manufacturing process. Triturations are often employed to achieve a homogeneous blend. A trituration is nominally 90- to 99-percent carrier or filler, which can lead to an undesirable increase in tablet weight and size. If the formulator has the option of distributing the micronutrients uniformly by combining them with other necessary ingredients in a larger granulation matrix, this can reduce the amount of inactive ingredients in the final dosage, enabling the formulator to achieve a lower tablet weight and size or a smaller capsule. Incorporating a granulation step can also help with quality assurance (QA) of the final product. The combination of multiple micro-nutrients into a granulation matrix allows testing of a single marker ingredient to verify homogeneity of the blend.
If the formulator carefully reviews the characteristics of and differences between each component prior to writing the formula, potential problems with active ingredient uniformity, manufacturing productivity and product compliance can be identified early in the product development process. Improved powder flow, more uniform distribution of active ingredients throughout the blend and finished dosage form, and masking of troublesome properties such as stickiness in production can all be effectively addressed by selectively incorporating problem-causing ingredients with other raw materials in the formula into a granulation matrix. By considering this strategy and working with an expert granulation partner, product development and commercialization can be accelerated, and the result can be a more productive commercial process.
Ken Abramowitz is the technology manager in Huber Engineered Materials' health and nutrition business unit (Huber.com).
About the Author
You May Also Like