High-Efficiency Tablet Coating Aids GMP Compliance for Supplement Manufacturers
April 19, 2010
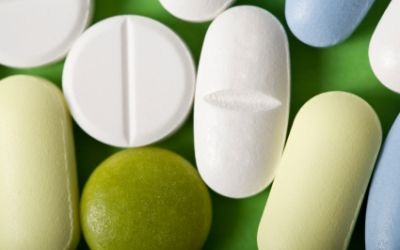
by Martin Hack
Compliance with GMPs (good manufacturing practices) is paramount for nutraceutical manufacturers seeking to produce high-quality dietary supplements. This is especially true for companies struggling with batch-to-batch consistency and contamination during tablet manufacturingtwo common challenges to GMP compliance.
By July 2010, all manufacturers developing dietary supplements and nutraceuticals for sale in the United States will need to comply with federal GMPs. While the cost of compliance is high$38,000 to $61,000 a year by FDA estimatestablet manufacturers can recoup that operational expense over the long term by investing in high-efficiency tablet coating equipment that will allow them to produce high-quality products with fewer defects, while actually increasing production speed.
The most advanced tablet coaters on the market are engineered with current GMPs in mind. From tablet pan design to spray technology, these machines have the ability to reduce processing times by up to 35 percent. By decreasing production times, manufacturers can operate with fewer tablet coaters, making it easier to meet GMP standards for this part of the manufacturing process.
Better Batch Consistency
The biggest limitation of traditional tablet coaters is the uniformity they can achieve. Tablet consistency is a large factor in quality control and time to market for tablet-based supplements. Typically, for a cosmetic coating, manufacturers can get uniform tablets, but inefficiently. More time and coating solution are required, increasing the operational costs of the manufacturing process.
For example, with conventional coaters, tablet weight must increase 4 percent to 5 percent to achieve a uniform coat. But the newest cosmetic coaters achieve the same coverage with only 1.5- to 2-percent weight gain. Additionally, advanced tablet coating technology can achieve a 4-percent coefficient of variation, which is better than any traditional machine.
High uniformity is also achieved through another technical advantage of new coaters, the mixing system. To get high uniformity, tablets must be adequately mixed. The most advanced system uses spiral baffles to move tablets constantly through the coating pan. One of the baffles moves tablets to the back of the pan, while the other brings them forward. In 10 minutes or less, manufacturers can attain tablet homogeneity in each batch.
The New Shape of Tablet Pans
The tablet pan may seem like a basic component of a coater, but its role in increasing the efficiency of nutraceutical campaigns is important. Different sizes and shapes of the pan can affect the number of defects in a batch.
Traditional tablet pans are short in length and large in diameter. This creates a thick tablet bed when solids are put in the coater. However, a zone exists in the middle of the tablet bed that is slow-moving, and tablets in that area do not get exposed to the surface of the bed as often. That means the process takes longer and uses more coating solution.
High-efficiency coaters have coating pans that are longer in length, but smaller in diameter. Because the tablet bed is spread wider, there is no slow-moving zone. The tablets are in constant motion, so they enter the spray zone more often for higher efficiency and better uniformity.
The smaller diameter pan also helps prevent twinning, which is when tablets stick together in the tablet bed. These tablets must be sorted out, and often are counted as rejects, affecting overall batch efficiency. When the tablet bed is thinner in the narrow pan, the tablets stay in motion, thus preventing twinning. This is especially valuable to manufacturers creating supplements as elongated or flat tablets, which are more likely to stick together than round tablets.
Eliminating Spray Drying
Traditional tablet coaters send air flow from the top or side of the coater, across the spray zone, through the tablet bed and out. However, bringing hot air into direct contact with spray as it is airborne will dry part of the solution before it hits the tablet surface.
If you look into a conventional coater during the process, you can see a cloud-like effect where the coating spray meets turbulent air and spreads the solution out, causing it to cover the pan and spray arms instead of the tablets. This wastes coating material and causes loss of tablets when they stick to the pan or spray solutions gets trapped in the machines filter system.
With advanced coating technology, air flow enters the coater from beneath the tablet bed, and it is distributed over the entire length of the pan. All air flow through the tablet bed is in the direction of flow, leaving no hot air in the spray zone. Spray drying becomes almost non-existent.
By eliminating spray drying, manufacturers will reduce coating solution waste. Thats because when air flow partially dries a droplet of coating material, it has a tendency to bead on the tablet pan instead of disperse on the tablets. This leads to an increased use of coating solution for each campaign. New tablet coaters ensure droplets are wet when they hit the tablet surface, resulting in less coating solution to achieve cosmetic uniformity.
Reduced Clean-up
Manufacturers want to campaign batches together until they absolutely need to stop. High-efficiency coaters reduce the amount of wasted coating solution left on the tablet pan and spray arms, so manufacturers can campaign longer without stopping to clean.
Less cleaning also helps boost overall company efficiencies in terms of waste management. A typical coater wash cycle uses 400 gallons of water. Because newer coaters require fewer cleanings, manufacturers potentially can save thousands of gallons of water and reduce wastewater processing each month.
Furthermore, because high-efficiency coaters do not waste as much solution, manufacturers wont need to change filters as often. All coaters have dust collectors or filter systems to catch solidified solution that does not make it onto the tablets. With an inefficient machine, expensive filters require frequent replacing, increasing manufacturing operating costs.
As the market for dietary supplements continues to grow, and FDA continues to enforce more stringent GMPs, manufacturers would be wise to explore options for increasing tablet coating efficiency. By producing more tablets with fewer defects, manufacturers can reduce their time to market and more quickly see a return on investment (ROI) for advanced tablet coating equipment.
As vice president and general manager of L.B. Bohle LLC, Martin Hack oversees all of the companys operations in North America and Puerto Rico. He holds a bachelor of science in electrical engineering from Virginia Polytechnic Institute and State University. For more information about L.B. Bohles tablet coating technologies, visit Bohle-Tablet-Coater.com or e-mail [email protected].
You May Also Like