Animal Nutrition Insights Magazine: Six Essential Best Practices in Controlling Microbiological Pet Food Safety
From ingredient handling to production methods to rigorous testing, a handful of best practices can help manufacturers in their quest to offer safe, quality dry pet foods.
September 11, 2014
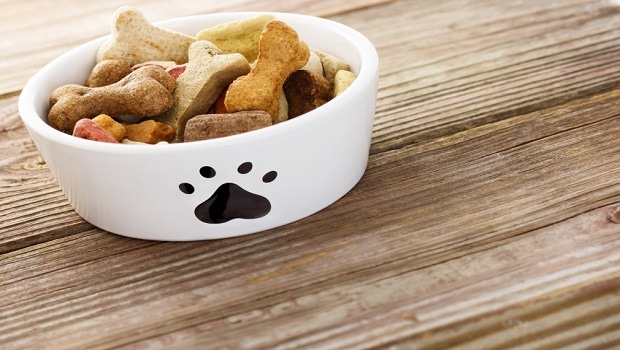
After a number of very public recalls, consumers and regulatory officials are paying closer attention to practices in the pet food industry. Historically, many of the ingredients for pet food have come from the scraps from other food plants and were of questionable microbiological quality. Many pet food extrusion factories have been converted from feed mills or other similar buildings with dry pet food equipment being retrofitted into the existing space. Currently, new factories are being built from the ground up to accommodate the expanding pet food market, as well as diets incorporating meat, vegetables and other wholesome ingredients. In either circumstance, the pet food manufacturing environment is directly impacted by the details of facility design and diet ingredients. Many of these new specialty diets (i.e., health-condition specific, grain-free, protein-specific, etc.) further diversify the overall microbiological challenges of pet food manufacturing. Although the challenges faced by the pet food industry are wide-ranging, there are some constants every manufacturer will encounter.
The free report, “Six Essential Best Practices in Controlling Microbiological Pet Food Safety," outlines a handful of best practices to help manufacturers in their quest to offer safe, quality dry pet foods.
One of the most crucial elements is monitoring the environment, which includes determining and documenting whether the processing environment is in microbiological control. Beyond post-sanitation swab samples, environmental control means having an awareness of every aspect of the production environment: equipment surfaces, water, air, and the materials moving in and out of the environment.
Other areas of paramount importance include monitoring ingredients, validating methods, mapping and managing workflow, and implementing an appropriate finished product hold/release testing program.
Authors Edward R. Richter, Ph.D., and Jessica L. Dyszel, Ph.D., are founder and director of research/laboratory, respectively, at Richter International Inc. They conclude the report by highlighting the importance of establishing a culture of critical thinking at all levels of production and quality control.
To read the free report, visit animalnutritioninsights.com.
You May Also Like